News
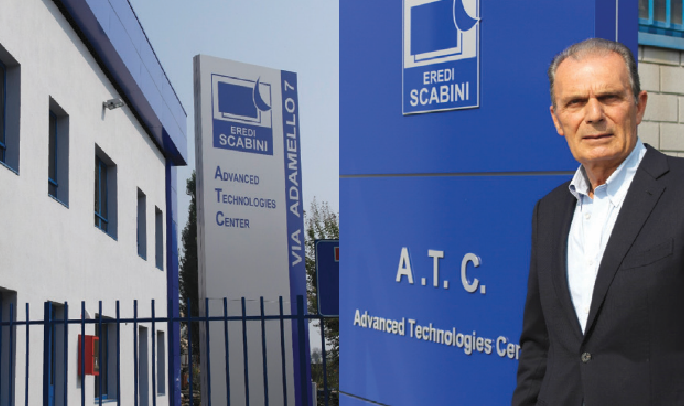
The new Advanced Technologies Center
and CEO Daniele Scabini.
Eredi Scabini reasserts is pioneering spirit by creating the Advanced Technologies Centre (ATC), a new company division entirely dedicated to the research and development of new products and technologies, as well as the design of constantly more innovative, high-performing refractory linings.
With state-of-the-art equipment, the new ATC has been built next door to the headquarters to house professionals with vast experience, including engineers, chemists and designers, who interact and collaborate every day, on an organised basis, to create/generate products and services of excellence.
The new ATC’s existence is grounded in the concept – strongly rooted in the company’s mentality – that no two projects are alike, and so every project deserves to be developed with the aid of all the know-how and resources available to the company; in other words, not research for its own sake, but as a means to achieve the aims set on the basis of the customer’s specific requirements.
The ATC is the place the company also likes to define as the “Home of Ideas”, because it brings together the important – not to say fundamental – branch of the company in which every new project is born, under a single roof.
But the ATC is also the function that interfaces with the company’s production side and sales function to oversee projects throughout their whole lives, monitoring their progress and ensuring that every step takes place in accordance with the set aims.
By creating the ATC, Eredi Scabini intends to consolidate its position as segment leader and to offer the refractory market products and services with high value added.
This is a real mission, rooted in the firm intention to build an increasingly close relationship with its customers, based on the offering of exclusive products and services which are more and more specific and deliver higher and higher performances.
The ATC is the jewel in crown of Eredi Scabini, which will be proud to offer a guided tour to all those interested.
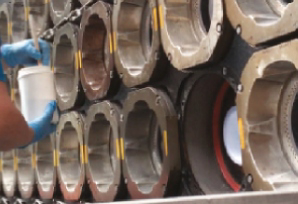
(Transition-plates treated with Becoat® WB 1000).
The ever-increasing demands being placed on Aluminium components in areas such as weight reduction or higher mechanical strength have resulted in the need to develop more sophisticated alloys as well as reliable casting processes.
Such developments require intelligent solutions – not just in terms of refractory materials, but also in their surface protection through the use of special coatings.
Whether ingot casting or continuous casting, the Eredi Scabini range offers custom-designed solutions for every application – productive, reliable and efficient.
BEcoat® is the Eredi Scabini’s family of Boron Nitride coatings for the Aluminium industry.
BEcoat® products are aqueous suspensions with high concentration of Boron Nitride specifically developed for molten metal applications. Metals and ceramic materials coated with BEcoat® are easier to clean and last longer thanks to the excellent lubricating and non-wetting properties of Boron Nitride combined with special nano binders and additives.
BEcoat® WB 1000, the last born, has been specifically developed for coating transition plates for Aluminium billets casting. The product can also be used in other applications in Aluminium, Zinc and Magnesium industries on ceramic materials in contact with molten metals to prevent corrosion and make the cleaning easier. In addition to the excellent lubricating and ‘non-wetting’ properties of Boron Nitride, special nano-additives provide good adhesion.
BEcoat® WB 1000 is available concentrated -to be diluted- or ready to use and can be applied by spraying or paintbrush.
Further information on the BEcoat® full range is available on our website.
With the hundreds of proprietary formulations (of our own invention!) in our catalogue, we believed that, over time, we had built up an offering broad enough to guarantee the best solution for all – or almost all – customers’ needs in the aluminium industry.
However, since it is not in our nature to “rest on our laurels”, observing the changes in the market we realised that we could do even more, and even better.
So, about 3 years ago, we launched a project to reassess our products specifically for aluminium, which involved the performance of more than 600 corrosion tests on 49 refractory castables, with four different alloys (46000/46100;5083;7075; 2196) at four different temperatures (815-1100-1200 and 1300°C).
An analysis of the huge amount of data generated by the tests revealed that our offering guaranteed excellent coverage of both standard and heavy-duty applications, but from the commercial point of view it was less competitive in intermediate applications (e.g. reverberatory furnaces with medium-power regenerative burners). There was therefore a gap in our range for a more specific product for these applications, which would enable us to offer customers an alternative to our “high-end” products.
Therefore, starting from an existing product family, which provided a well tried and tested base, our R&D department developed a new technology, capable of delivering better performances in terms of resistance to thermal shock and corrosion resistance at higher-than-standard temperatures.
A better compromise, if possible at the same price as the existing refractory.This was no easy task: the alumina content was not to be increased in order to avoid higher reversible linear changes and lower thermal shock resistance, and the exclusive use of “non-wetting” additives in the matrices to reduce corrosion and provide better resistance to high temperatures had to be avoided. Without a doubt, efforts had to be concentrated on the matrix, which in these castables accounts for 40-50% of the total weight.
Once again nanotechnology, which we have already been using for more than 15 years, came to our aid. The combination of techniques and knowledge of chemistry and physics which enables to manipulate matter at the atomic level to create structures with size measured in nanometres enabled us to add neutral, solid nanoparticles to the matrix, to block the pathways in the matrix by means of which the molten metals usually saturate the refractory, thus making it “aluminium-proof”.
These particles have immense specific coverage: just one gram of material is able to cover an area of 800m2. Since the number of particles needed to obtain our required result is minimal and our production know-how allows them to be evenly distributed even through large masses, their effect on the final cost of the product is negligible.
This technique has provided the basis of new products with protection against corrosion and corundum penetration at high-temperature up to 90% higher than the equivalent standard product. Corrosion resistance is so high and the quality-price ratio so excellent that we have decided to create a whole family of these products: Alproof®.
The following is the comparison between the corrosion resistance of Alproof® and the equivalent standard product.
As the data show, in normal conditions (at 815°C) both products give excellent results, but from 1.100°C to 1.200°C there is 90% less corrosion on Alproof®.
However, our regular customers should note that its physical properties and installation procedures are very similar to those of the well-established Flustone® products.
We expect that this new, beneficial discovery will prove very popular with our customers!
Daniele Scabini
2018 Trade fairs
12th World Trade Fair & Conference, 9 – 11 Ottobre 2018 – Messe Düsseldorf, Germania.
Eredi Scabini sarà lieta di accogliere i visitatori allo stand n. 10G45
Eredi Scabini Srl and the German-based Henze BNP AG, specialist for boron nitride products, signed a strategic cooperation agreement for the development and distribution of boron nitride coatings.
Increasing aluminium component requirements, such as weight reduction or increased load-bearing capacity, necessitate special alloys and casting processes in cast aluminium. Simultaneously, this development requires new solutions in the field of refractory products and their protection with special coatings. As an answer to this challenge, the Eredi Scabini/Henze cooperation will bundle both companies’ know-how and their many years of experience to offer customised solutions and an optimal service to their customers. Particular in the areas of product development and global distribution, both companies will cooperate closely. The products, primarily ceramic coatings with a high share of boron nitride, will be distributed by Eredi Scabini under the brand name BEcoat® WB.
“Thanks to the close cooperation with Eredi Scabini, resources are bundled in the sales and marketing sector. By means of this, we can offer our customers optimal solutions and service worldwide,” Matthias Henze, chairman of Henze BNP AG emphasises. “We are looking forward to the cooperation with Henze. The ceramic coatings are the ideal match for our product line. This way, we can offer our customers perfectly aligned systems,” says a delighted Corrado Scabini, Sales and Marketing director of Eredi Scabini.
About the product:
BEcoat®: Advanced boron nitride coatings for aluminium Industry.
BEcoat® products are aqueous suspensions with a high concentration of Boron Nitride specifically developed for molten metal applications.
Metals and ceramic materials coated/treated with BEcoat® are easier to clean and last longer thanks to the excellent lubricating and non-wetting properties of Boron Nitride combined with special nano binders and additives.
BEcoat® is available concentrated – to be diluted – or ready to use, in different colors, and can be applied by spraying or paintbrush.
Main features:
- Protects metals, ceramics and graphite from corrosion
- Inhibits corundum and slag growth on refractory linings
- Excellent lubricating and release properties
- High adhesion and good abrasion resistance
- Easy application by spraying or with paintbrush
- Water-based, physiologically safe / environmentally friendly products
- Pre-heating is recommended
- Colored products available for easier visualization
BEcoat® line includes:
BEcoat® WB 100
BEcoat® WB 200
BEcoat® WB 300
BEcoat® WB 330
It is the company’s highly quality-oriented policy, continuous innovation in its product line, and, above all, its ability to offer custom solutions based on specific demands that have placed Eredi Scabini at the top, as a well-known and highly-appreciated partner around the world.
This year, for the first time, the company will participate as an exhibitor at IRAN METAFO 2017, in Hall 7, Stand B03 (held in Tehran, December 4 to 7, 2017).
2016 Trade fairs and conferences with the participation of Eredi Scabini
EEC 2016 – 11th European Electric Steelmaking conference & Expo, 25-27 May 2016 – Venice – Italy
ALUMINIUM 2016 – 11th World Trade Fair & Conference, 29 November/1 December 2016 – Messe Düsseldorf, Germany.
We will be pleased to meet you at booth n. 10G45
Yesterday, today and tomorrow: we offer opportunities, never just products.
2015 is a very important year for Eredi Scabini for many reasons. First and foremost because it is celebrating 70 years of successful, thriving business and constant growth.
The merit for this lies first of all with the founder, Osvaldo Scabini, who made this magnificent company possible, and then with his heirs and their many fine inspirational ideas, which over the years have earned the company a reputation for top-grade quality and services. Customers have also played a key role, and not only in terms of sales figures. Their problems and their needs have provided the necessary stimulus for the development of more and more important products and projects.
Successful products such as the CPS® (Crucible Pre-formed System) and ABT® (Advanced Block Technology), together with our most famous monolithics, such as Flustone® and Histone®, were developed in just this way, and then went on to actually change the whole approach to refractories. Today the new Nanoplast® products are once again revolutionising the fundamentals of our sector; one example is the new IPS™ (Inductor Preformed System) project, which is opening out unprecedented management options for foundries.
The fact that we are now celebrating our first 70 years of prosperous business is also thanks to all the employees who have worked for our company over time with dedication, commitment and team spirit.
It was with them and their families that Eredi Scabini chose to share the joy of this major milestone, by organising a party at the company’s main site. A day of pleasure and enjoyment for young and old, with games, cooking sessions and magic shows, not to mention singing and dancing performances by the participants themselves. During the day, guests were also able to view all the company’s production departments.
2015 is now drawing to an end, and – in spite of the considerable current difficulties – this year we are once again very satisfied with the results achieved. Because, as company Chairman Daniele Scabini reminds us: “Here at Eredi Scabini – today as in the past – we offer customers opportunities, never just products.”
And the story goes on …